Understanding the Latest Trends in Welding and Fabrication
Introduction to Modern Welding and Fabrication
In recent years, welding and fabrication have witnessed significant advancements, driven by technological innovations and changing industry demands. As these fields continue to evolve, professionals must stay abreast of the latest trends to remain competitive and efficient. With new materials, techniques, and tools emerging, the landscape of welding and fabrication is transforming rapidly.
The integration of technology in welding and fabrication has not only improved precision but also enhanced productivity. From automation to the use of advanced materials, these trends are reshaping the industry, offering numerous benefits to manufacturers and fabricators worldwide.
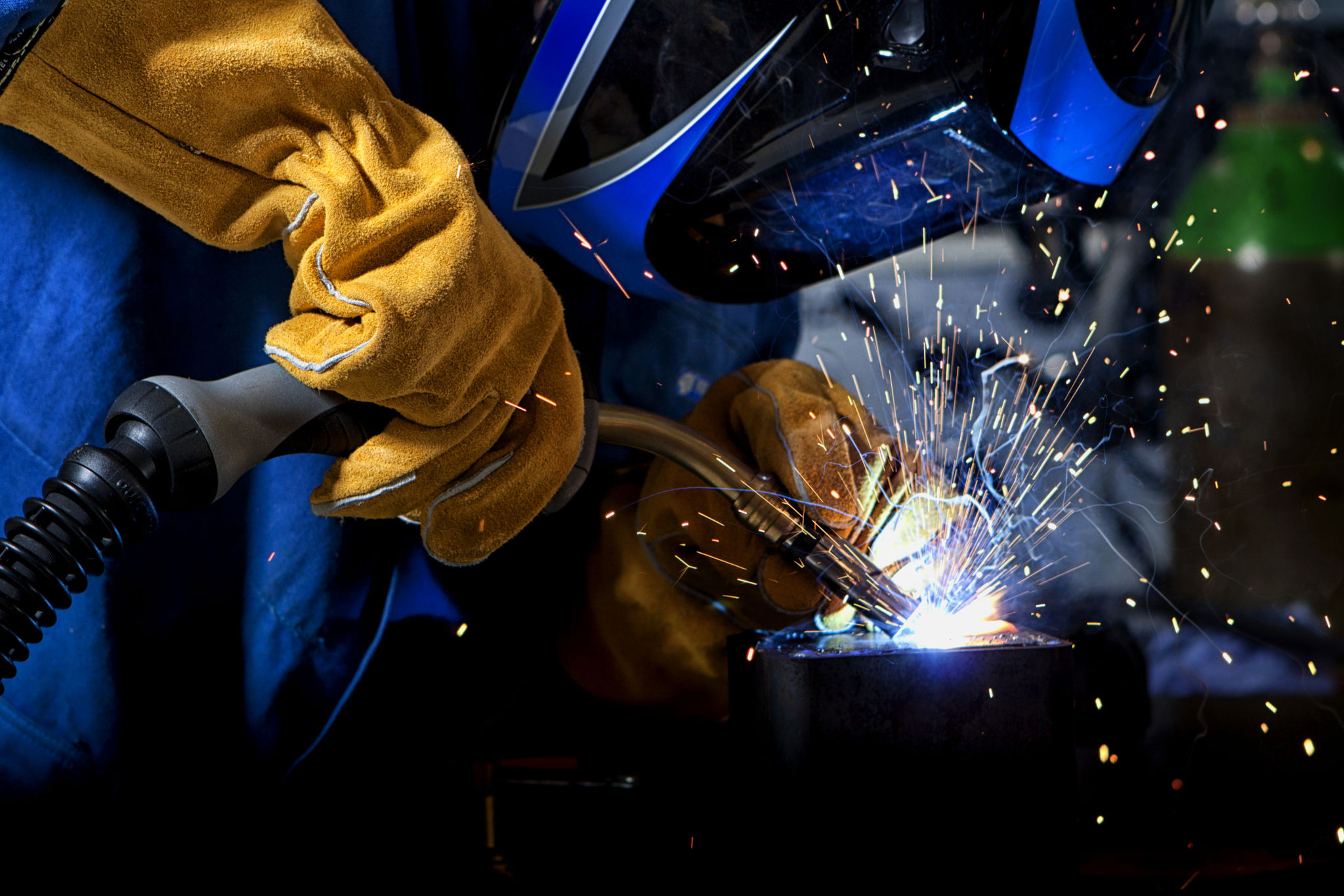
Automation and Robotics in Welding
The introduction of automation and robotics into welding processes has revolutionized the industry. Automated welding systems are now capable of performing tasks with unparalleled accuracy and speed. These systems reduce the likelihood of human error, leading to higher quality outputs and increased safety on the job site.
Robots equipped with artificial intelligence are now able to learn and adapt to different welding tasks, making them incredibly versatile. This adaptability allows for greater flexibility in production lines, enabling companies to switch between projects with ease.
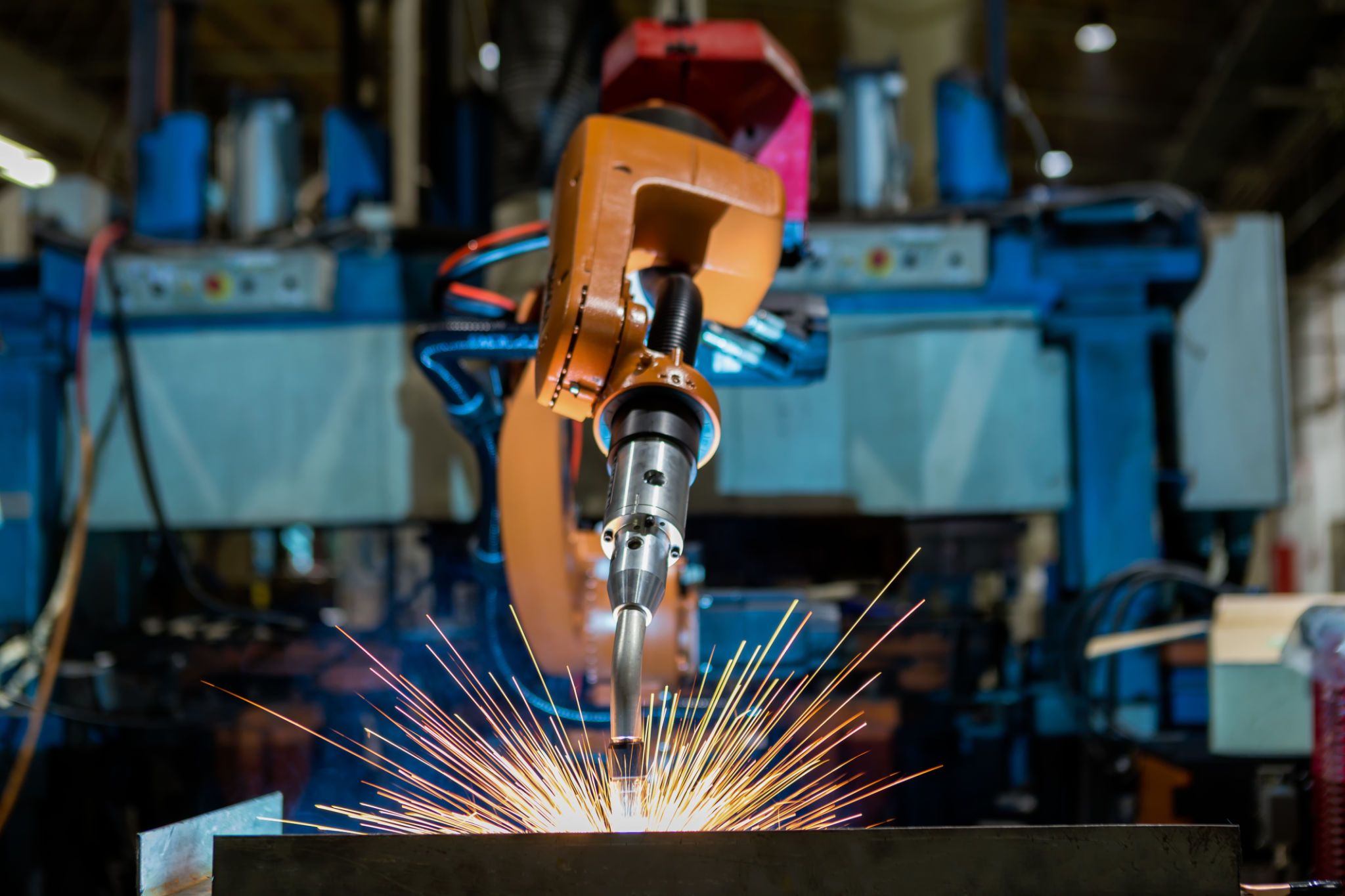
Advanced Materials and Techniques
Welding and fabrication are no longer limited to traditional materials like steel and aluminum. The use of advanced materials such as carbon fiber composites, titanium alloys, and high-strength steels is becoming increasingly common. These materials offer superior strength-to-weight ratios, making them ideal for industries like aerospace and automotive.
Innovative welding techniques such as friction stir welding and laser welding have also gained popularity. These methods provide enhanced joint strength and reduced distortion, which are critical in applications requiring high precision.
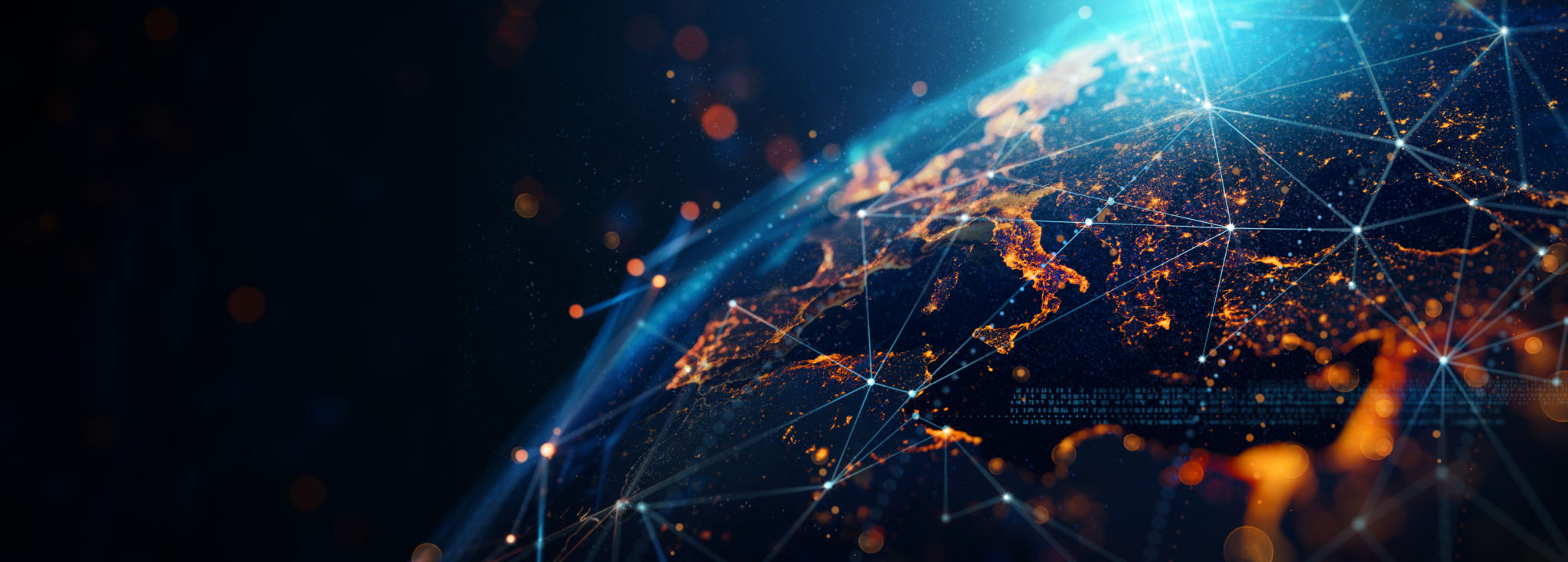
Sustainability in Welding and Fabrication
As environmental concerns grow, the welding and fabrication industry is focusing more on sustainability. This involves adopting practices that reduce waste and energy consumption. For instance, using recycled materials and optimizing processes to minimize resource usage are becoming standard practices.
Furthermore, companies are investing in eco-friendly technologies that lower emissions during fabrication processes. This not only helps meet regulatory standards but also aligns with global efforts to reduce carbon footprints.
Enhanced Safety Measures
Safety remains a paramount concern in welding and fabrication. Recent trends emphasize the development of advanced safety gear and monitoring systems that protect workers from hazards. Wearable technology, including smart helmets and gloves, provides real-time data on environmental conditions and worker health metrics.
Moreover, improved training programs incorporating virtual reality simulations allow workers to practice skills in a controlled environment before applying them in real-world scenarios. This approach reduces accidents and enhances overall safety awareness.
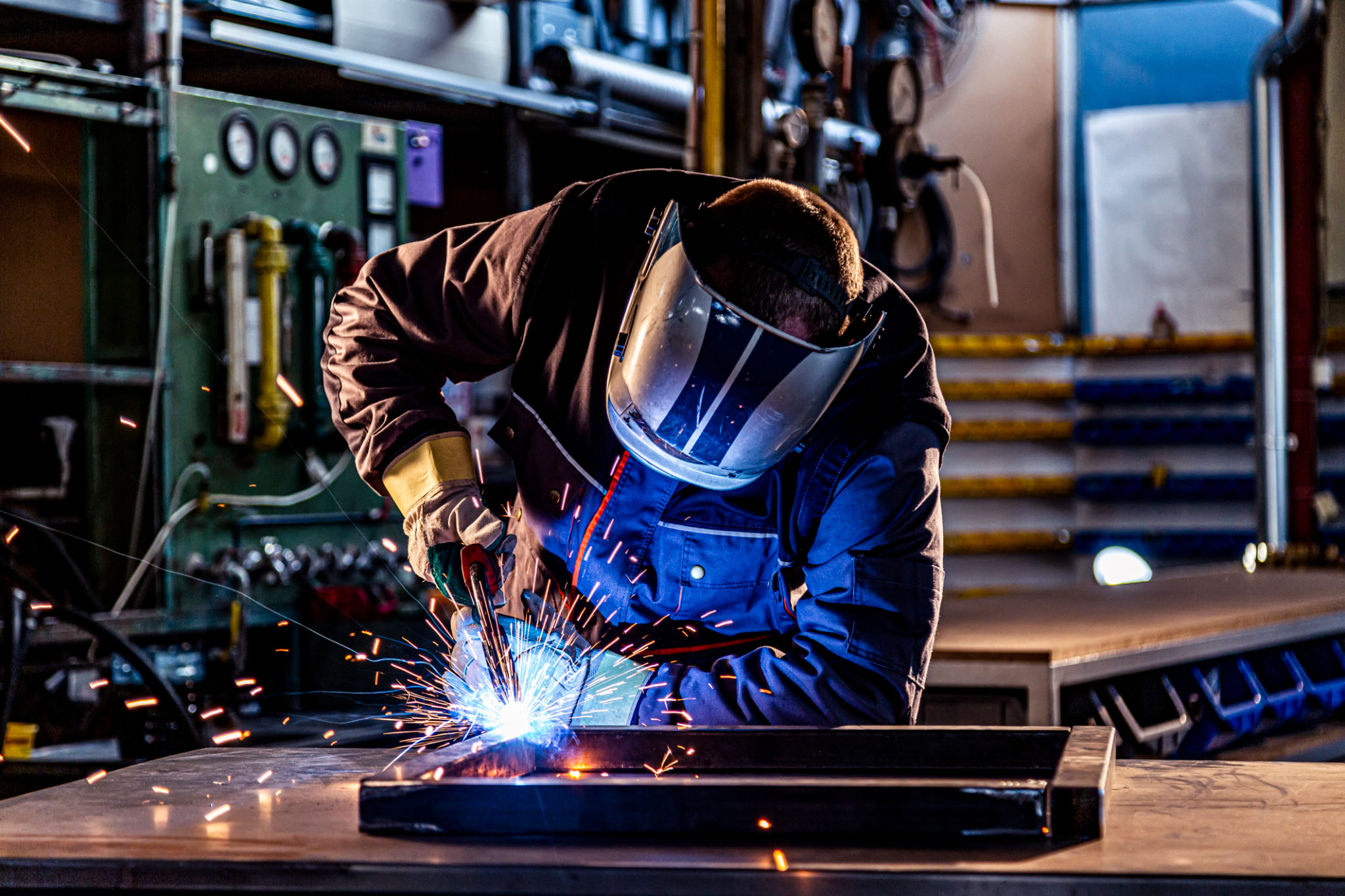
The Future of Welding and Fabrication
Looking ahead, the welding and fabrication industry is set to embrace even more technological advancements. The integration of the Internet of Things (IoT) will enable smart factories where machines communicate seamlessly to optimize production processes.
Furthermore, innovations in additive manufacturing, such as 3D printing, offer exciting possibilities for custom fabrication. These technologies promise to redefine how products are designed and produced, allowing for greater customization and reduced lead times.
In conclusion, staying informed about the latest trends in welding and fabrication is crucial for professionals seeking to thrive in this dynamic industry. By embracing new technologies and sustainable practices, businesses can enhance their operations while contributing positively to the environment.