The Future of Welding and Fabrication: Trends to Watch in the Industry
Introduction to the Evolving Welding Industry
The welding and fabrication industry is experiencing a significant transformation, driven by technological advancements and changing market demands. As we look to the future, several key trends are shaping the landscape, promising to redefine how welding professionals work and innovate. Embracing these trends will be crucial for businesses aiming to stay competitive and efficient.
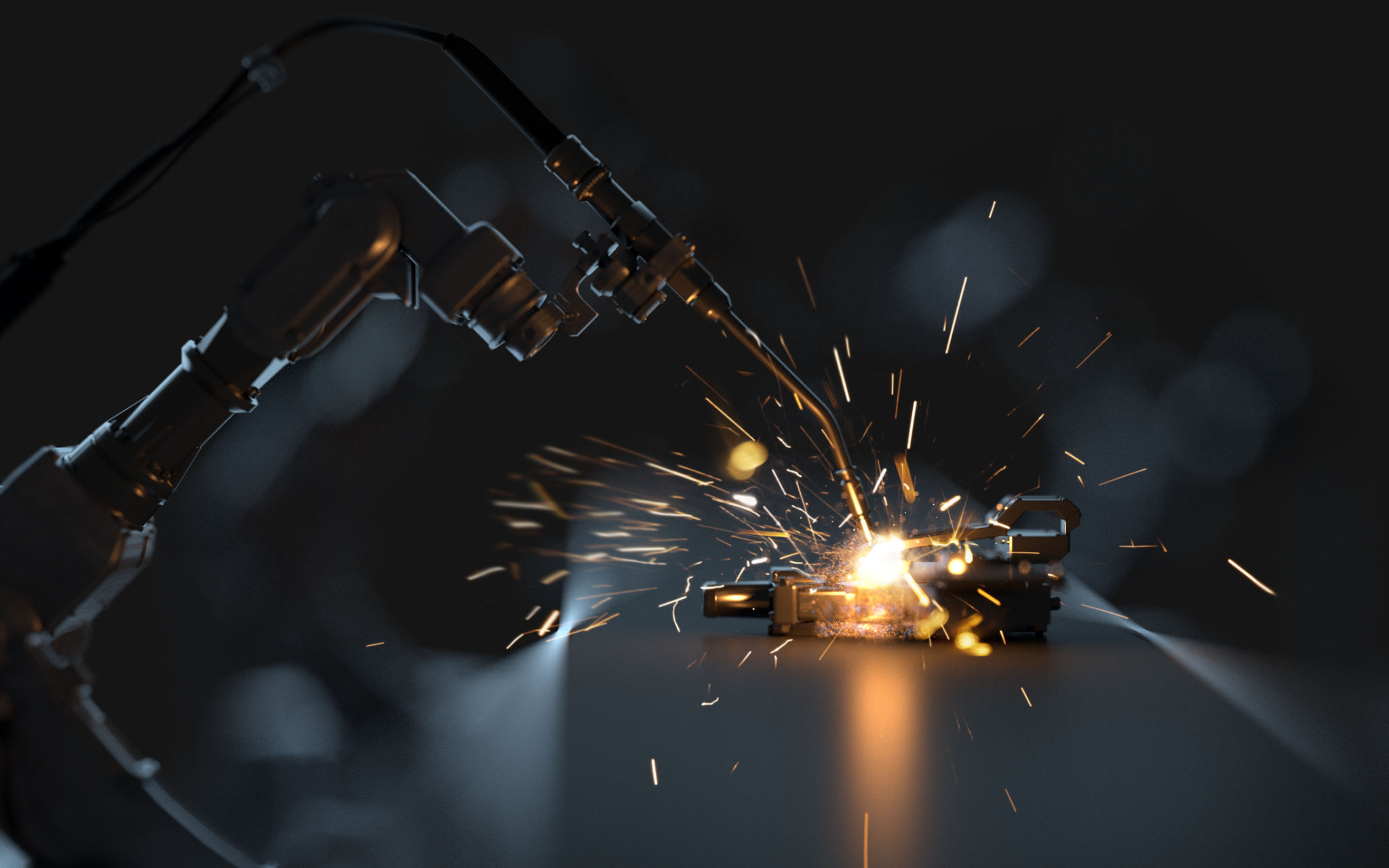
Automation and Robotics in Welding
One of the most notable trends is the increasing use of automation and robotics. Robotic welding systems are becoming more prevalent, offering enhanced precision, speed, and efficiency. These systems can handle repetitive tasks, reducing human error and increasing production rates.
Moreover, advancements in artificial intelligence (AI) are enabling robots to adapt and learn from their environments. This adaptability means that robotic systems can be integrated into various welding applications, from automotive manufacturing to aerospace projects. As these technologies continue to evolve, we can expect even more sophisticated robotic solutions in the industry.
Adoption of Advanced Materials
The demand for lightweight yet strong materials is also influencing welding practices. Industries such as automotive and aerospace are increasingly turning to advanced materials like carbon fiber composites and high-strength alloys. These materials pose unique challenges for welders, requiring specialized techniques and equipment.
To meet these demands, welding professionals must stay informed about new materials and invest in appropriate training and tools. This will ensure they can effectively work with cutting-edge materials and maintain high standards of quality and safety.

Emphasis on Sustainability
Sustainability is becoming a key focus across all industries, including welding and fabrication. Companies are seeking eco-friendly practices to reduce their carbon footprint and minimize waste. Welding processes that use less energy or produce fewer emissions are gaining traction.
Additionally, the recycling of materials is being prioritized. Welders are encouraged to explore techniques that allow for the reuse of materials without compromising structural integrity. As environmental regulations tighten, sustainable practices will become increasingly important in maintaining compliance and promoting a positive brand image.
Integration of Digital Technologies
Digital technologies are revolutionizing how welders plan, execute, and evaluate their work. Tools such as augmented reality (AR) and virtual reality (VR) are being used for training purposes, providing immersive learning experiences that enhance skill development without the risk of real-world errors.
Furthermore, the use of digital twins—virtual replicas of physical assets—allows for real-time monitoring and optimization of fabrication processes. This integration of digital technologies not only improves efficiency but also enhances the ability to predict maintenance needs and prevent costly downtimes.
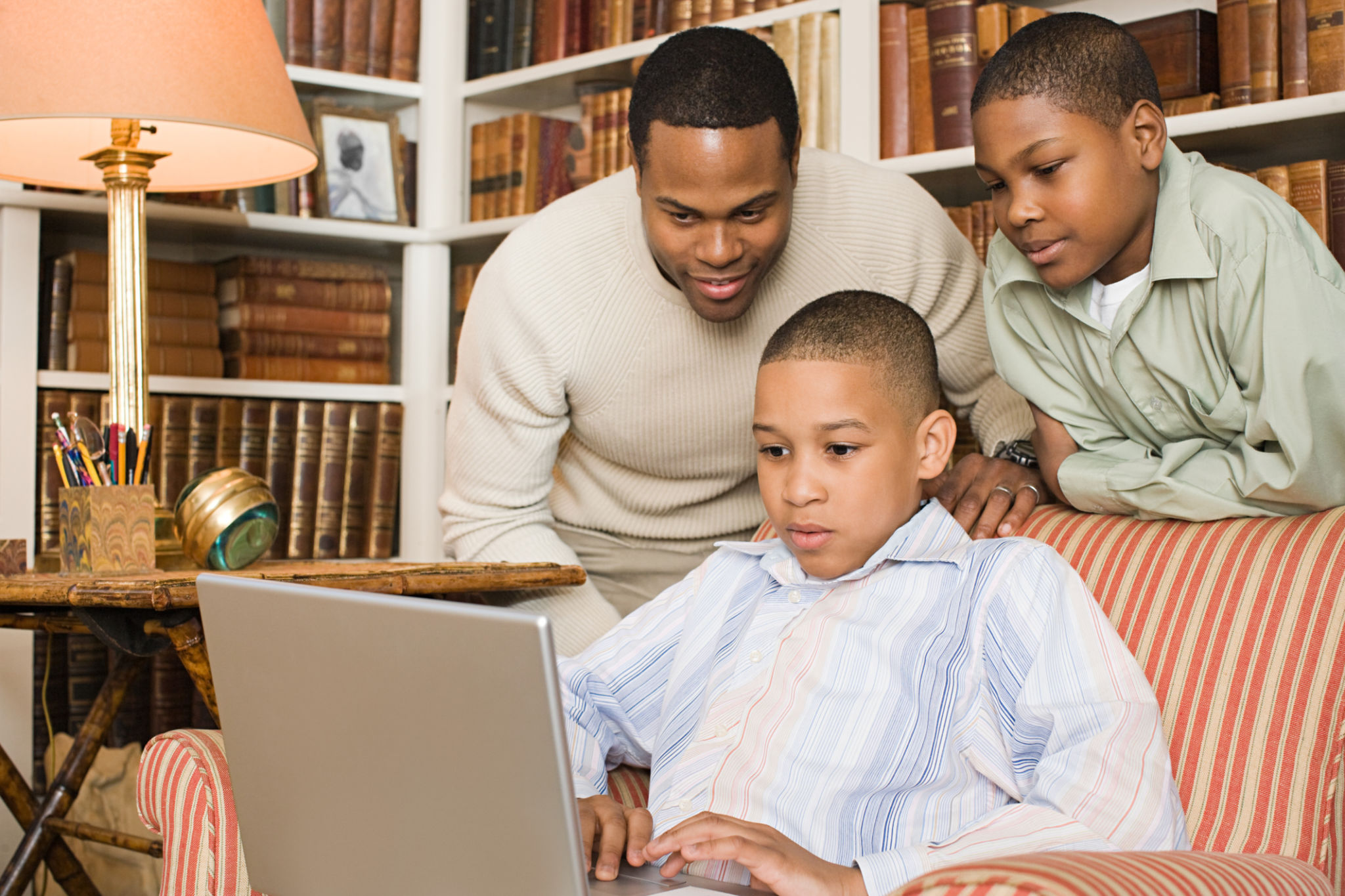
Conclusion: Preparing for the Future
The future of welding and fabrication is bright, with numerous opportunities for growth and innovation. By staying informed about emerging trends such as automation, advanced materials, sustainability, and digital technologies, industry professionals can position themselves for success.
As these trends continue to develop, businesses that adapt quickly will gain a competitive edge. Investing in education, training, and technology will be essential for navigating the changing landscape and capitalizing on new opportunities in the welding industry.