Sustainable Metal Fabrication Techniques for Modern Welders
Introduction to Sustainable Metal Fabrication
In recent years, the metal fabrication industry has increasingly focused on sustainability, aiming to reduce environmental impact while maintaining high-quality production. Modern welders are at the forefront of this movement, adopting innovative techniques that prioritize efficiency and eco-friendliness. By integrating sustainable practices, welders can contribute to a greener future without compromising on the strength and durability of their work.
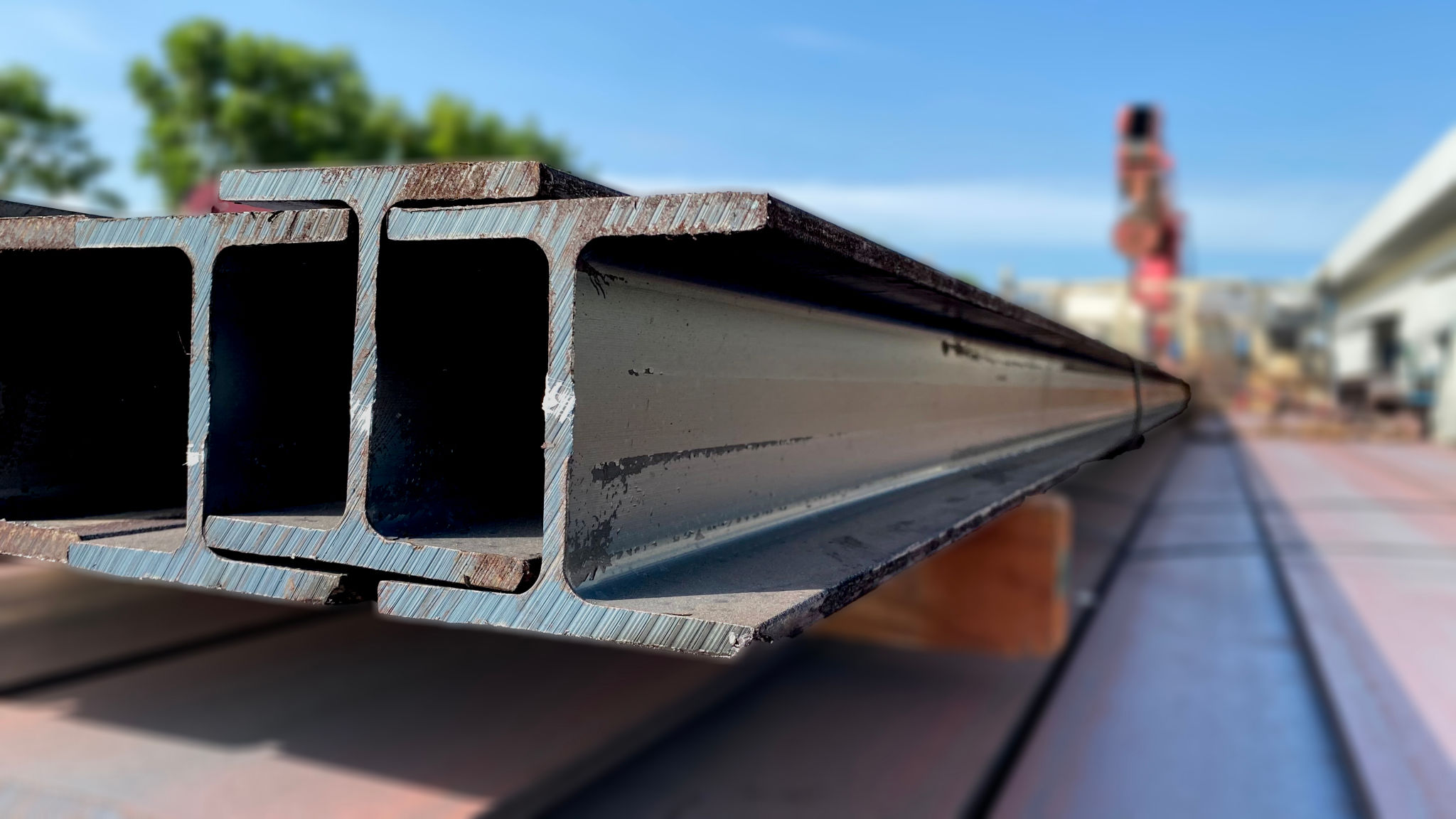
Why Sustainability Matters in Metal Fabrication
The traditional metal fabrication process often involves substantial energy consumption and waste production. As global awareness of environmental issues grows, there is a pressing need for industries to minimize their carbon footprint. Sustainable metal fabrication techniques not only help in conserving resources but also offer cost savings and improved workplace safety. Embracing these methods can also enhance a company's reputation as an environmentally responsible business.
Reducing Waste Through Efficient Design
One of the critical steps towards sustainable metal fabrication is reducing waste at the design stage. By employing techniques such as computer-aided design (CAD) and finite element analysis (FEA), welders can optimize material usage, minimizing offcuts and scrap. This approach not only conserves resources but also reduces the cost associated with raw materials.
Recycling and Reusing Materials
Recycling is a cornerstone of sustainability in metal fabrication. By reusing scrap metal and other materials, welders can significantly reduce the demand for new raw materials. Implementing a systematic recycling process within a workshop ensures that all potential waste is either reused or recycled efficiently. This practice not only benefits the environment but also reduces disposal costs.

Energy-Efficient Welding Techniques
The welding process itself can be energy-intensive, but there are several techniques to improve efficiency. Methods such as laser welding, friction stir welding, and electron beam welding use less energy compared to traditional arc welding processes. Additionally, using energy-efficient equipment and machines can further reduce power consumption, contributing to overall sustainability efforts.
Leveraging Technology for Sustainability
Technology plays a vital role in advancing sustainable practices in metal fabrication. Innovations such as automated welding robots and IoT-enabled monitoring systems allow welders to optimize operations and reduce resource usage. By leveraging smart technology, welders can achieve precision and efficiency, leading to less waste and a smaller environmental footprint.
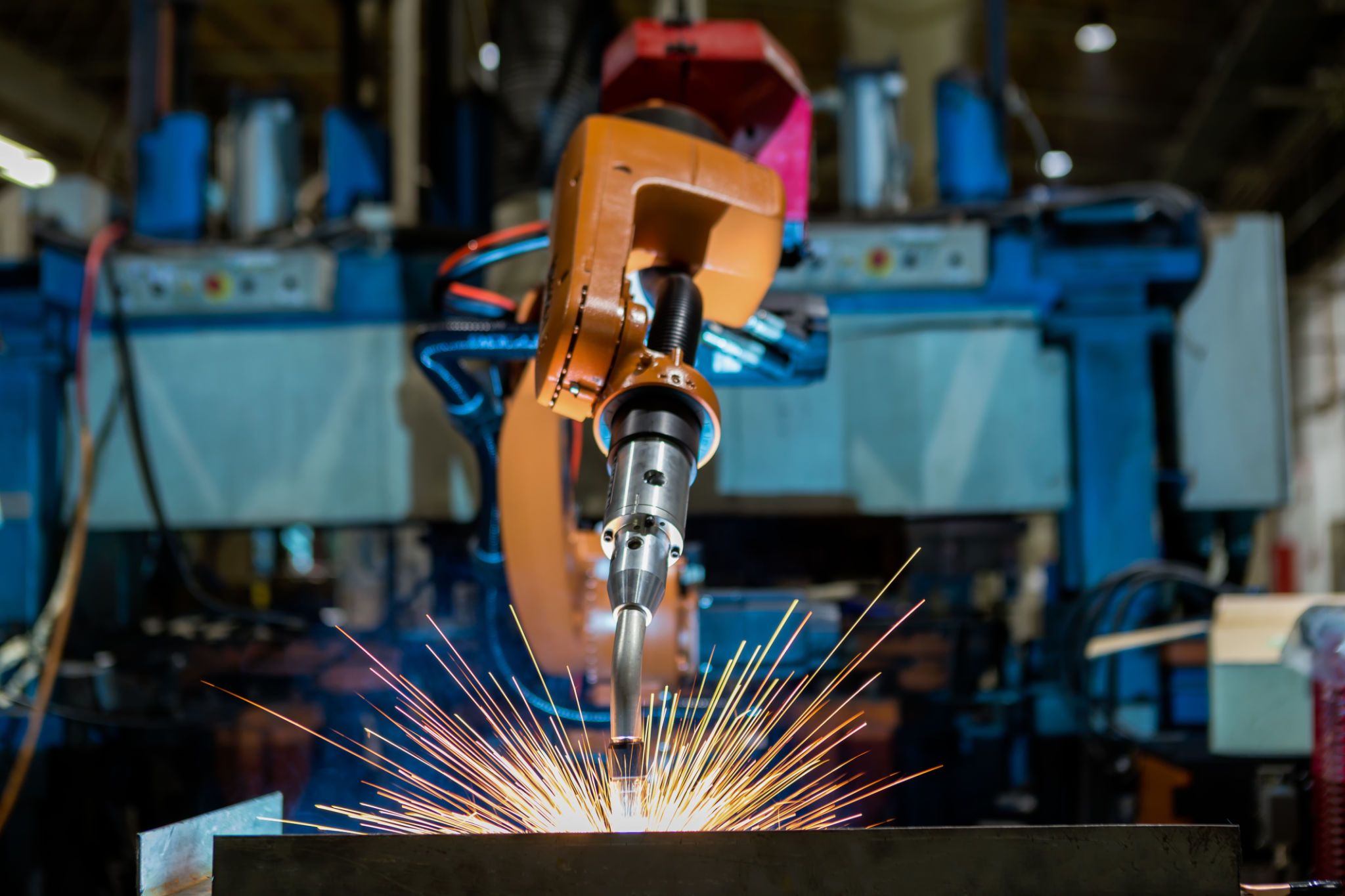
Training and Education for Sustainable Practices
For sustainable metal fabrication techniques to become widely adopted, it is essential to invest in training and education. Providing welders with the knowledge and skills needed to implement eco-friendly practices ensures that sustainability becomes an integral part of their work. Workshops, seminars, and online courses are excellent platforms for sharing information on the latest sustainable techniques in metal fabrication.
Conclusion: The Future of Metal Fabrication
Sustainable metal fabrication techniques represent the future of the welding industry. As more welders adopt these practices, the industry will continue to evolve towards a more environmentally responsible model. By focusing on waste reduction, energy efficiency, and technological advancements, modern welders can play a crucial role in shaping a sustainable future for metal fabrication.