Seasonal Welding Projects: Preparing for Winter Fabrication Challenges
Understanding Winter Fabrication Challenges
As the colder months approach, welding professionals face unique challenges that require careful preparation and adaptation. Winter fabrication projects demand a keen understanding of how low temperatures can affect welding processes and materials. The cold can lead to brittle welds, increased porosity, and other issues that could compromise the integrity of structures.
To combat these challenges, welders must adjust their techniques and equipment to ensure high-quality results. This involves not only understanding the effects of temperature but also implementing strategies to mitigate its impact.

Adjusting Techniques for Cold Weather
One of the primary adjustments for winter welding is preheating the materials. Preheating helps to reduce the cooling rate of the weld, which minimizes the risk of cracking. This is particularly important for thicker materials where temperature differentials can be more pronounced.
Additionally, maintaining a controlled environment is crucial. Setting up temporary shelters or enclosures around the welding site can shield the area from wind and moisture, both of which can adversely affect welding quality. Using windbreaks and tarps can help maintain a stable environment conducive to effective welding.
Choosing the Right Equipment and Consumables
Winter conditions necessitate careful selection of equipment and consumables. It is essential to use welding machines that are designed to operate efficiently in cold temperatures. Additionally, selecting the right electrodes and filler materials that can withstand lower temperatures without losing their effectiveness is vital.
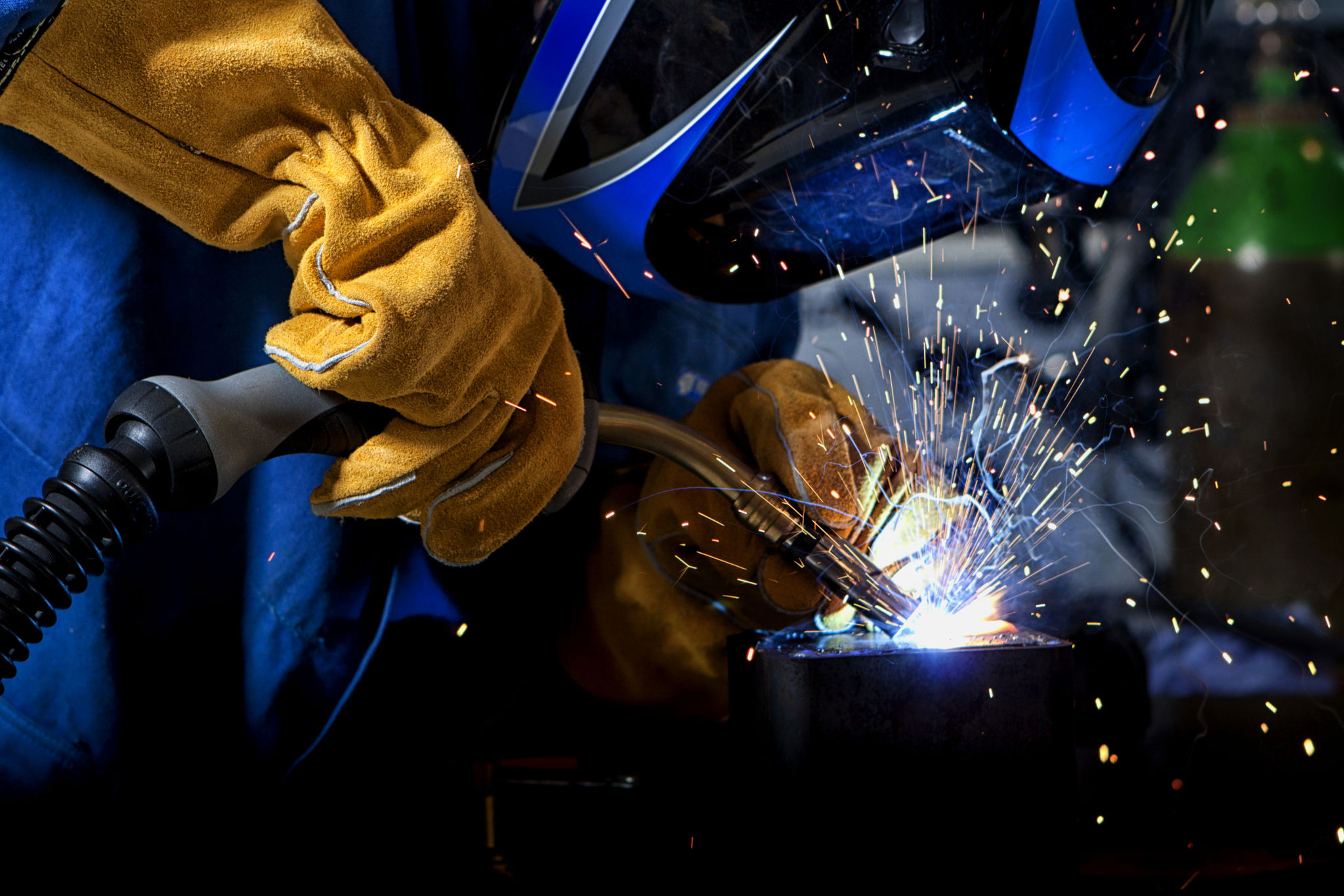
Consumables should be stored properly to prevent moisture absorption, which can lead to hydrogen-induced cracking. Keeping electrodes warm and dry is a simple but effective way to ensure they perform optimally during winter projects.
Safety Measures in Winter Welding
Safety is paramount in any welding project, and winter conditions introduce additional hazards. Slippery surfaces, reduced visibility due to shorter daylight hours, and the potential for hypothermia are all concerns that must be addressed.
- Ensure proper lighting in work areas to combat reduced visibility.
- Use non-slip mats or coatings on work surfaces to prevent accidents.
- Equip workers with appropriate cold-weather gear to maintain body heat.
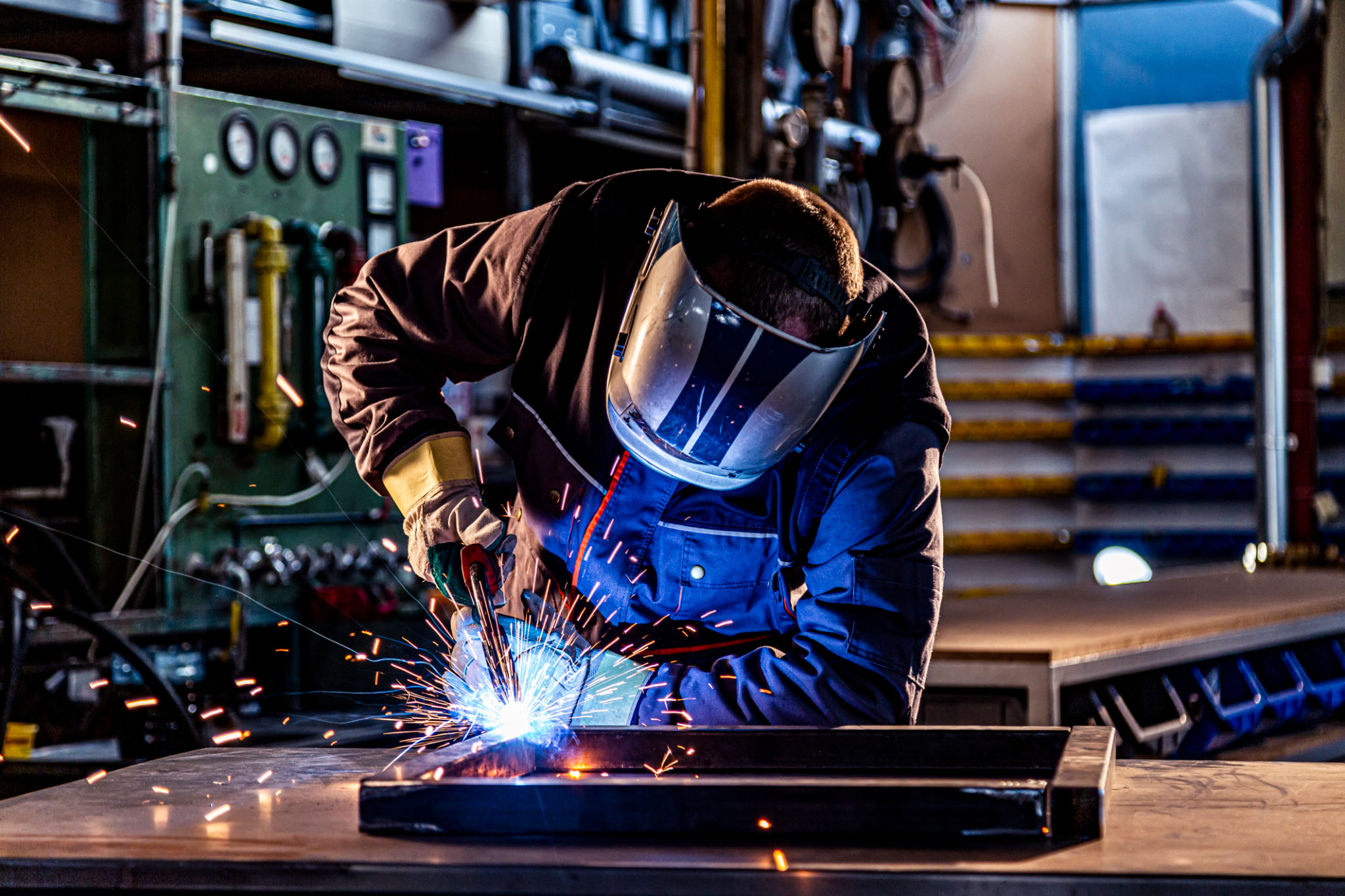
Training and Preparedness
Proper training is crucial for welding teams working in winter conditions. Workers should be educated on the specific challenges posed by cold weather and trained in techniques to address them. Regular safety briefings and drills can reinforce the importance of vigilance and preparedness.
Employers should also ensure that all safety equipment is in good condition and readily accessible. This includes emergency kits, first-aid supplies, and communication devices for workers operating in remote or isolated locations.
Conclusion: Embracing Winter Welding Opportunities
While winter welding projects come with their own set of challenges, they also present unique opportunities for skilled welders to showcase their expertise. By understanding the effects of cold weather on welding processes and implementing strategic adjustments, professionals can deliver high-quality results even in the harshest conditions.
Preparation is key to overcoming winter fabrication challenges. By focusing on proper techniques, equipment selection, safety measures, and continuous training, welders can ensure successful outcomes for their projects all year round.