Myth-Busting Common Misconceptions About MIG and TIG Welding
Understanding the Basics: MIG vs. TIG Welding
Welding is a crucial process in metal fabrication, and two of the most popular methods are MIG (Metal Inert Gas) welding and TIG (Tungsten Inert Gas) welding. However, despite their widespread use, these techniques are often misunderstood. This post aims to clear up some of the most common misconceptions surrounding these two welding methods.
MIG welding, also known as Gas Metal Arc Welding (GMAW), uses a continuously fed wire electrode and an inert gas mixture to protect the weld from contamination. TIG welding, or Gas Tungsten Arc Welding (GTAW), employs a non-consumable tungsten electrode and is ideal for precision work that requires clean and high-quality welds.
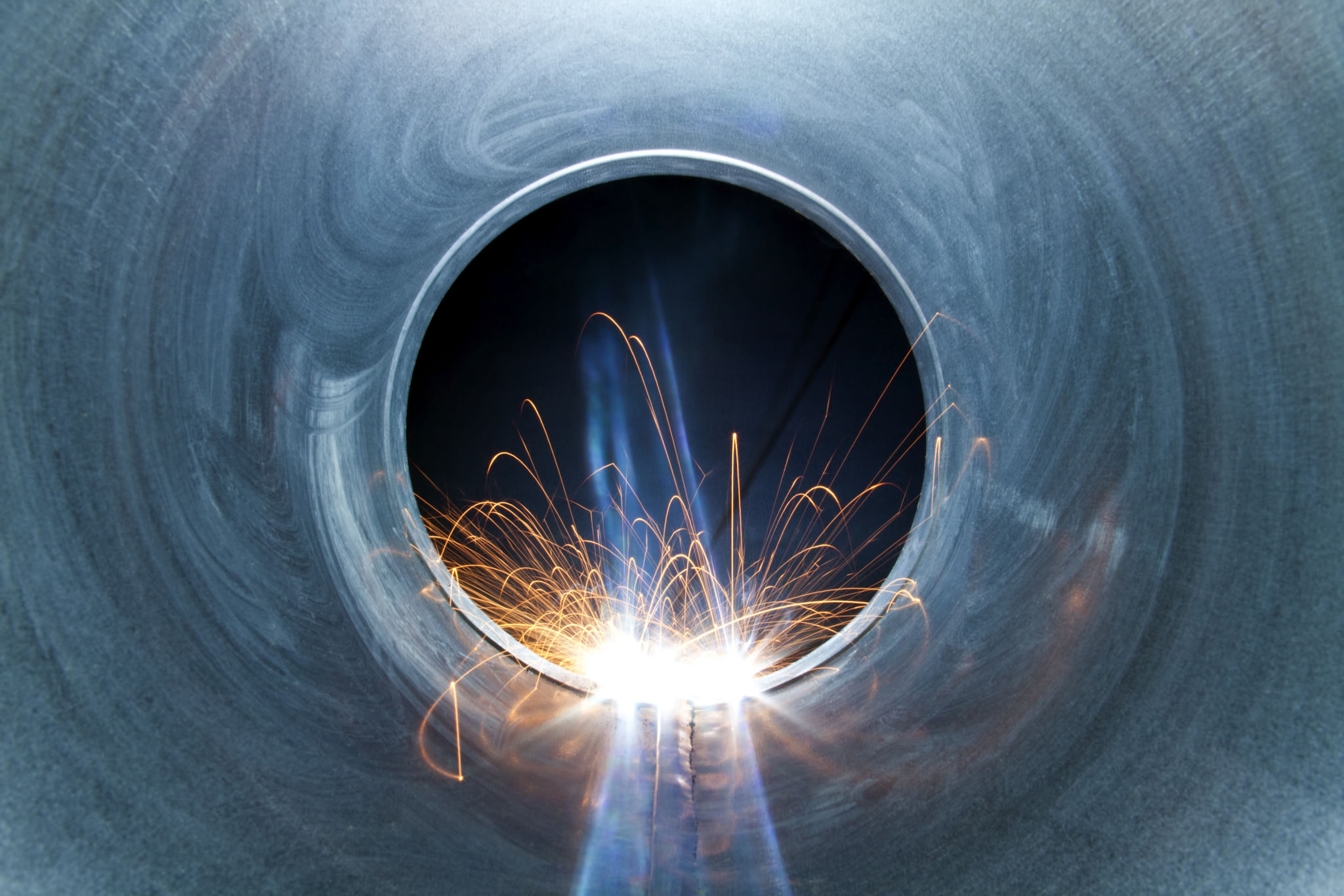
Myth: MIG Welding is Only for Amateurs
One of the prevalent myths is that MIG welding is solely for beginners or hobbyists. While it's true that MIG welding's relative ease makes it accessible to novices, it is also widely used in professional settings. MIG welding is valued for its efficiency and speed, making it a favorite in industries such as automotive manufacturing and construction.
Professionals appreciate MIG welding for its ability to weld thicker materials quickly, which is essential in high-production environments. Therefore, dismissing it as an amateur technique overlooks its significant industrial applications.
Myth: TIG Welding is Always Better
TIG welding is often heralded as the superior method due to its precision and control. However, this does not mean it is always the best choice for every project. The reality is that the right welding method depends on the specific requirements of the job. TIG welding is excellent for thin materials or projects needing a clean finish, such as aerospace or artistic applications.
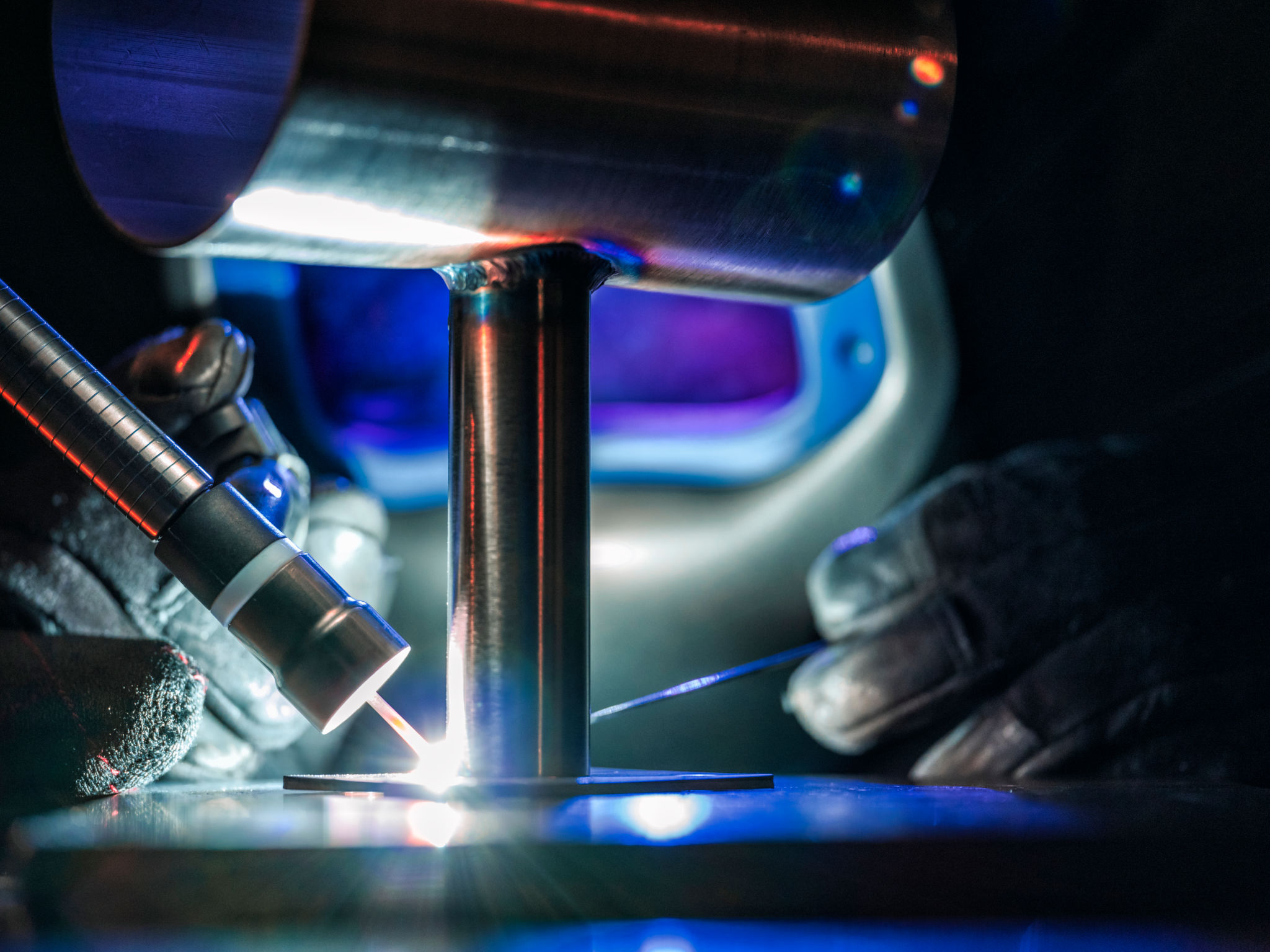
However, when working with thicker materials or when speed is a priority, MIG welding might be a more suitable option. Both techniques have their own strengths and are better suited to different tasks.
Myth: You Can Use Any Gas for Both Methods
A common misconception is that the same shielding gas can be used for both MIG and TIG welding. In reality, each method requires specific gases to optimize performance. MIG welding typically uses a mixture of argon and carbon dioxide, while TIG welding usually requires pure argon.
Using the incorrect gas can lead to subpar results, such as increased spatter or contamination in MIG welding, and poor arc stability in TIG welding. It’s essential to use the correct gas type to ensure high-quality welds.
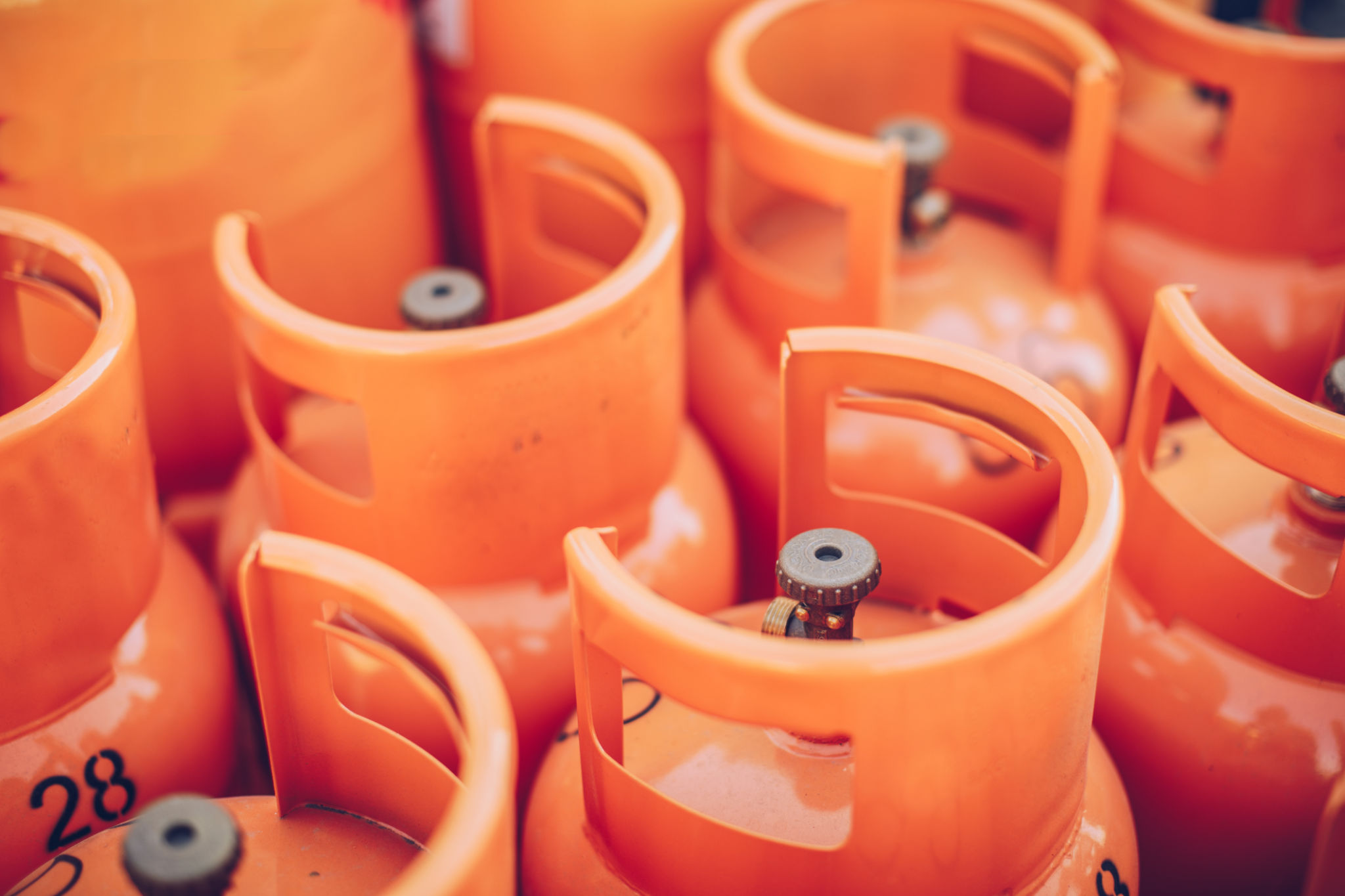
Myth: MIG and TIG Welding are Interchangeable
Another myth is that these two methods are interchangeable, which implies that one can easily switch between them without any differences in technique or setup. This is a misconception because each method has distinct characteristics that require specific skills and equipment adjustments.
MIG welding is generally faster and more forgiving of minor surface contaminants, while TIG welding demands a higher level of cleanliness and precision. Choosing between MIG and TIG should be based on the project specifications, including material type, thickness, and desired finish quality.
The Importance of Training and Experience
Both MIG and TIG welding require proper training and practice to master. While technology and equipment can aid in achieving better welds, the welder's skill plays a crucial role in the final product. Understanding the nuances of each method will help operators select the appropriate technique for their specific needs.
In conclusion, both MIG and TIG welding have their place in metal fabrication. By debunking these myths, we hope to provide a clearer understanding of each method's capabilities. Whether you’re a hobbyist or a professional welder, choosing the right technique will ensure successful outcomes for your projects.