Debunking Common Myths About Industrial Welding
Understanding the Basics of Industrial Welding
Industrial welding is a crucial part of many manufacturing and construction processes. Despite its importance, several myths persist about this intricate trade. Understanding the realities of industrial welding can help both professionals and laypeople appreciate the skill and precision involved.
Welding is not simply about fusing metals together. It involves a deep understanding of materials, techniques, and safety protocols. This article aims to debunk some of the most common myths surrounding this essential craft.

Myth 1: Anyone Can Weld
One prevalent myth is that welding is a simple skill that anyone can pick up quickly. In reality, welding is a specialized trade that requires extensive training and practice. Professional welders undergo rigorous training programs to learn how to work with different materials and techniques.
The skill set required for welding includes understanding the properties of various metals, knowing how to operate sophisticated machinery, and adhering to strict safety standards. Thus, it's not just about holding a torch; it’s about mastering an art form.
Why Training Matters
Proper training ensures welders can produce strong, reliable welds that meet industry standards. The quality of a weld can significantly affect the durability and safety of the finished product. Therefore, a trained welder's expertise is indispensable in ensuring structural integrity.

Myth 2: All Welding Is the Same
Another common misconception is that all welding processes are identical. In fact, there are several types of welding, each suited for specific applications and materials. The three most common types are MIG welding, TIG welding, and stick welding.
- MIG Welding: Also known as Gas Metal Arc Welding (GMAW), this method uses a continuous wire feed as an electrode and is ideal for thin to medium thickness metals.
- TIG Welding: Tungsten Inert Gas (TIG) welding involves using a tungsten electrode and is preferred for precision work on thin materials.
- Stick Welding: Also called Shielded Metal Arc Welding (SMAW), this method is versatile and effective for heavy-duty work.
The Importance of Choosing the Right Method
Choosing the correct welding technique is vital for ensuring the strength and appearance of the weld. Factors such as material type, thickness, and intended use must be considered to select the most appropriate method.
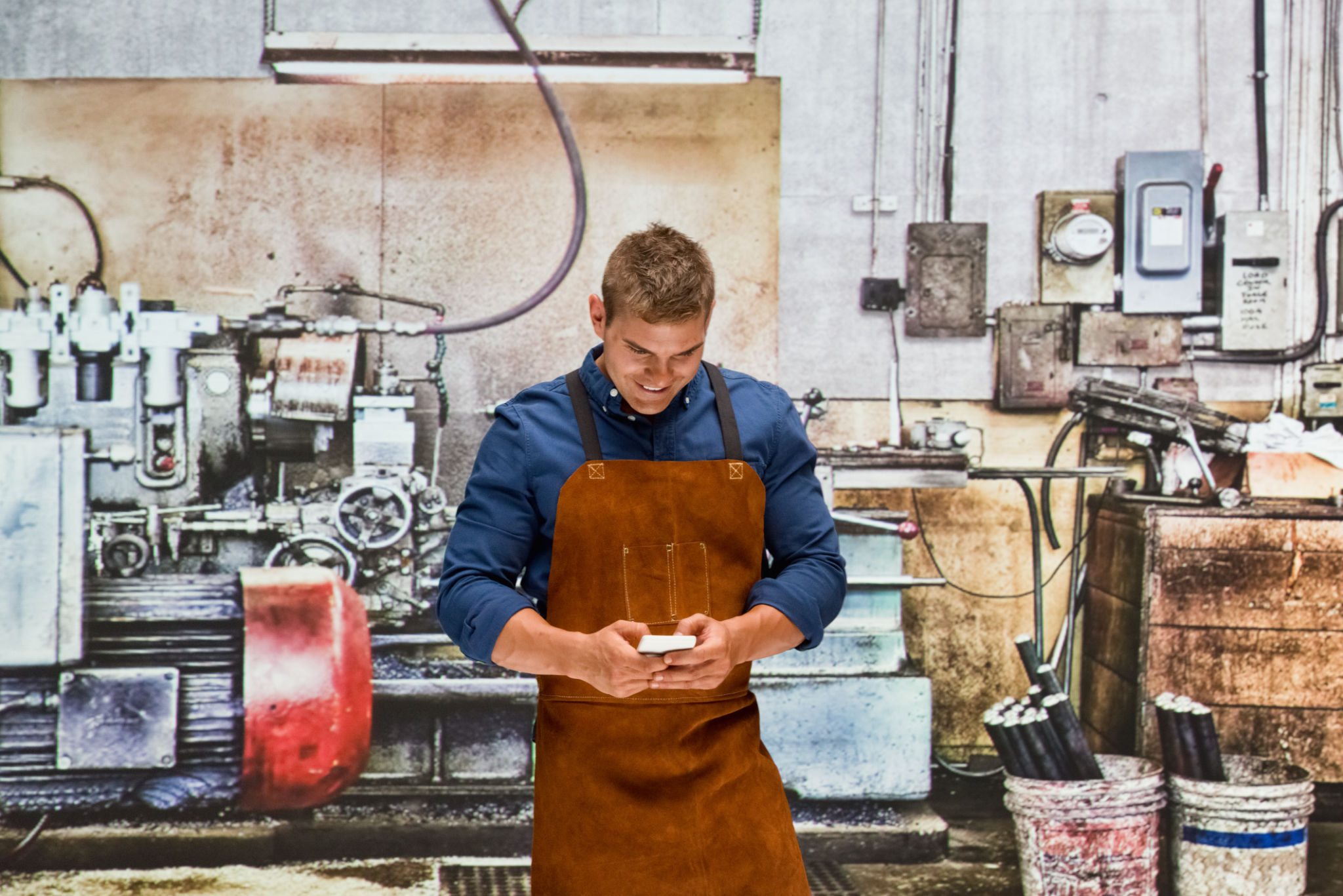
Myth 3: Welding Is Unsafe
While it's true that welding involves certain risks, it’s a myth that it is inherently unsafe. With proper training and adherence to safety protocols, welding can be performed safely. Modern safety equipment and practices have significantly reduced the risks associated with welding.
Welders are trained to use personal protective equipment (PPE) such as helmets, gloves, and protective clothing to safeguard against burns and exposure to harmful fumes. Regular maintenance of equipment also plays a critical role in ensuring a safe working environment.
Safety Measures in Place
Industries adhere to stringent safety standards to protect their workers. This includes regular safety training sessions, inspections, and the use of advanced safety gear. By following these measures, the risks associated with welding can be effectively managed.
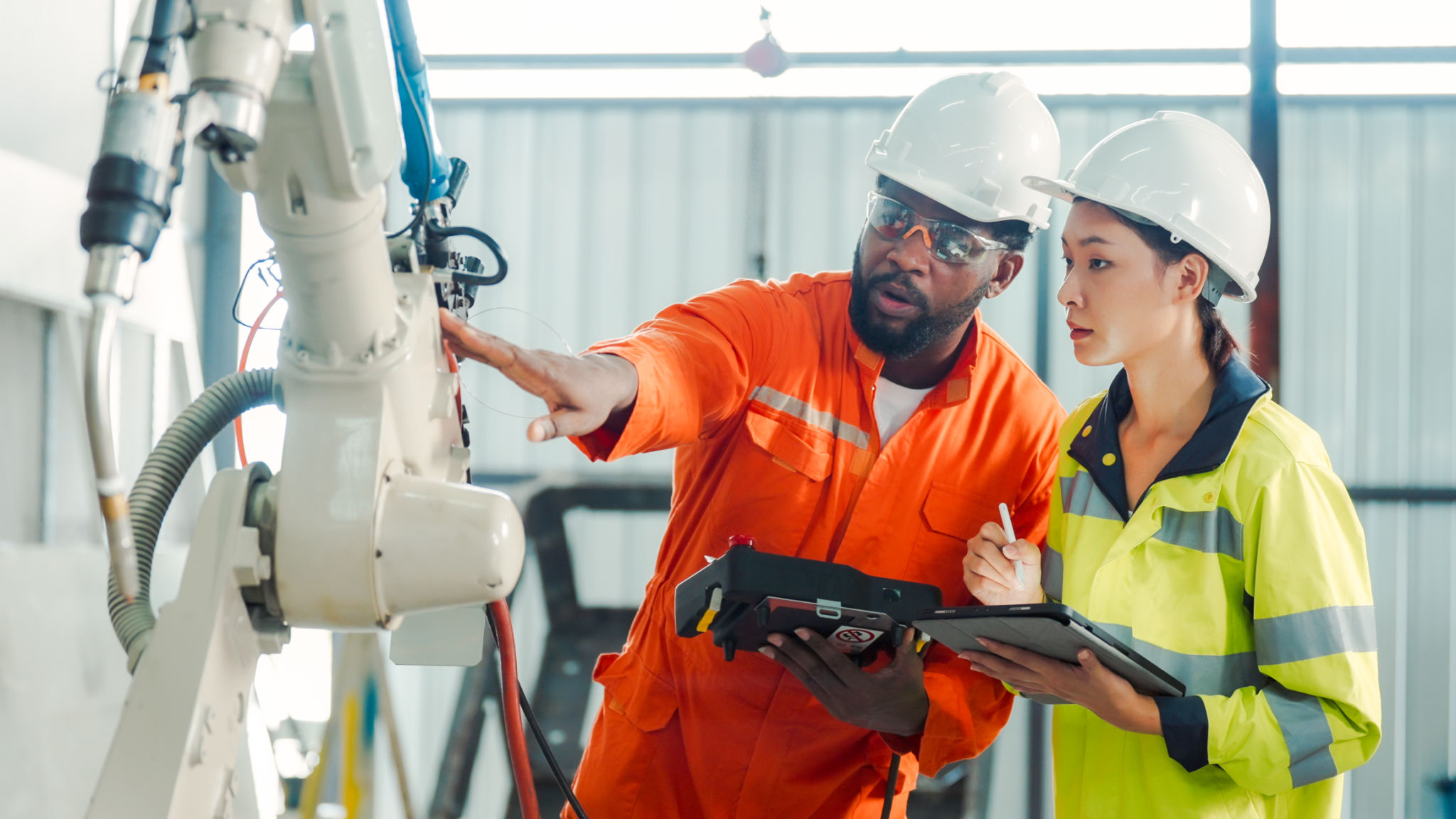
Conclusion: Appreciating the Craft of Welding
Debunking these myths helps in acknowledging the complexity and skill involved in industrial welding. Beyond just joining metals, it requires precision, expertise, and a commitment to safety. As industries continue to evolve, so too do the technologies and techniques used in welding, making it an ever-important field.
Recognizing the realities of industrial welding not only enhances our appreciation for welders but also underscores the crucial role they play in various sectors. Whether constructing skyscrapers or repairing vehicles, skilled welders are essential to building the world around us.