Common Misconceptions About Industrial Welding Solutions Debunked
Understanding the Complexity of Industrial Welding
Industrial welding is a critical process in manufacturing and construction, yet it is often surrounded by misconceptions. These myths can lead to misunderstandings about the capabilities, safety, and applications of welding solutions. By debunking these misconceptions, businesses can make more informed decisions about their welding needs.
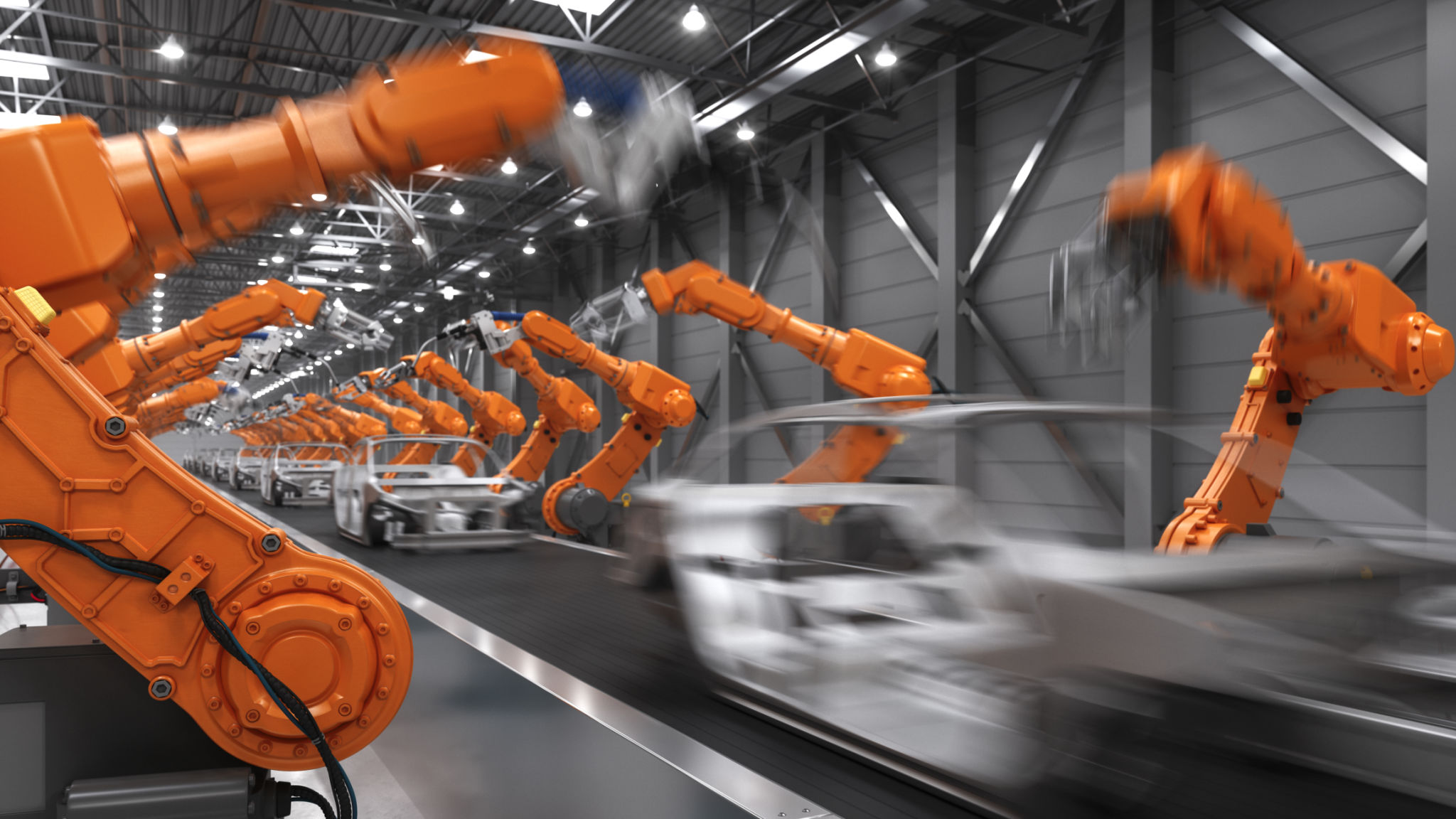
Misconception #1: Welding is a Simple Process
One common misconception is that welding is a simple task that can be performed by anyone with minimal training. In reality, welding requires a high level of skill and expertise. Professional welders undergo extensive training to understand the various techniques and materials involved. They must also be knowledgeable about safety protocols and the intricacies of different welding machines.
The complexity of welding techniques like TIG, MIG, and stick welding means that each method has its specific applications and challenges. It's not just about joining two pieces of metal; it involves understanding the properties of materials and how they react under heat.
Misconception #2: All Welds Are Created Equal
Another myth is that all welds are the same in terms of strength and quality. This is far from the truth. The strength and quality of a weld depend on multiple factors including the technique used, the skill of the welder, and the materials involved. For instance, a weld made with an incorrect technique or improper materials can result in weak joints that may fail under stress.
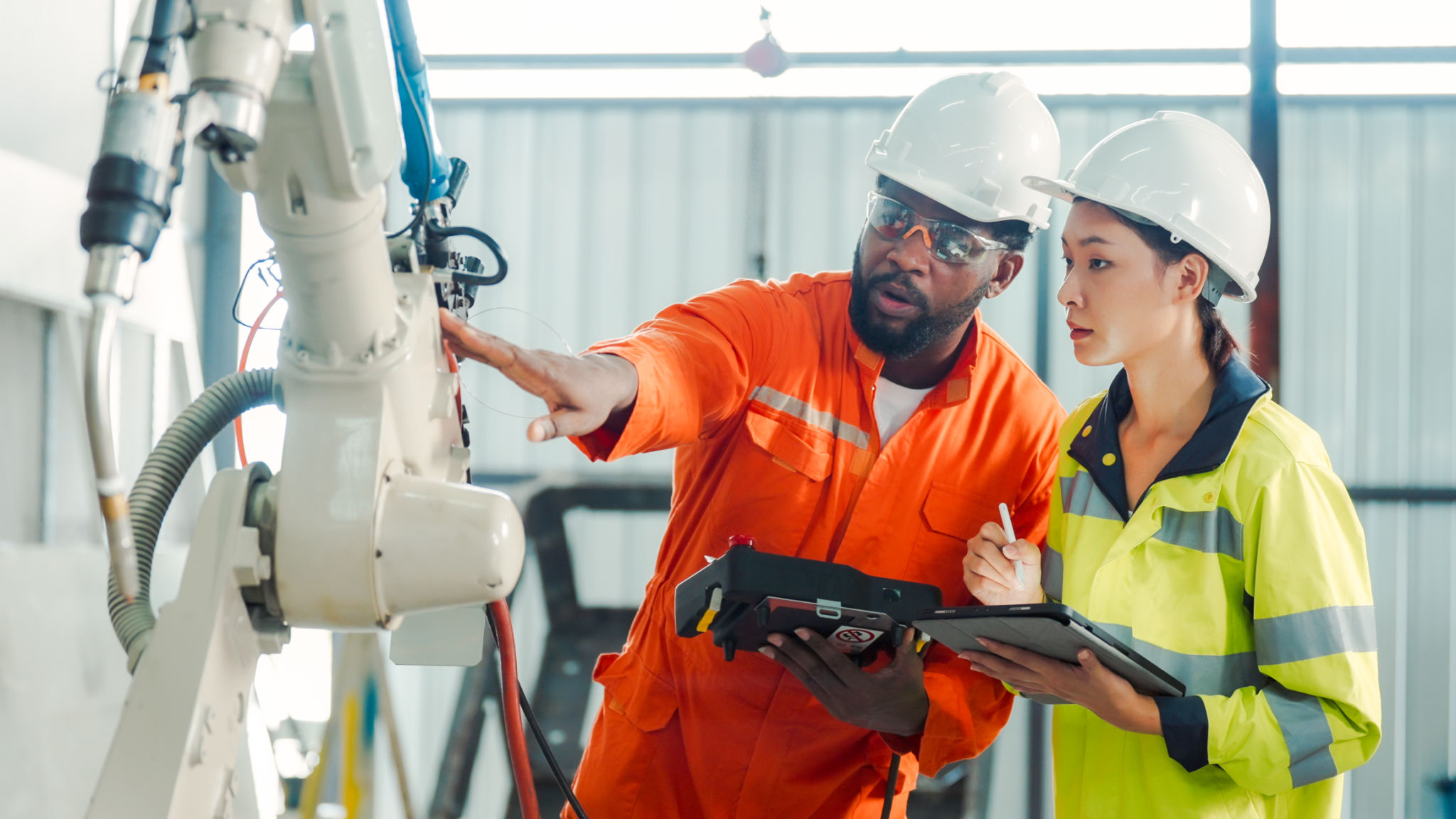
Quality control is essential in industrial welding to ensure that each weld meets the required standards. This often involves rigorous testing and inspection processes to detect any defects or weaknesses.
Misconception #3: Welding is Unsafe
While welding involves high temperatures and potentially hazardous materials, it is not inherently unsafe. Proper safety measures and equipment can mitigate most risks associated with welding. Professional welders are trained to use protective gear such as helmets, gloves, and aprons to protect themselves from burns, UV radiation, and fumes.
Moreover, modern welding equipment often includes advanced safety features like automatic shut-off systems and ventilation solutions to ensure a safer working environment.
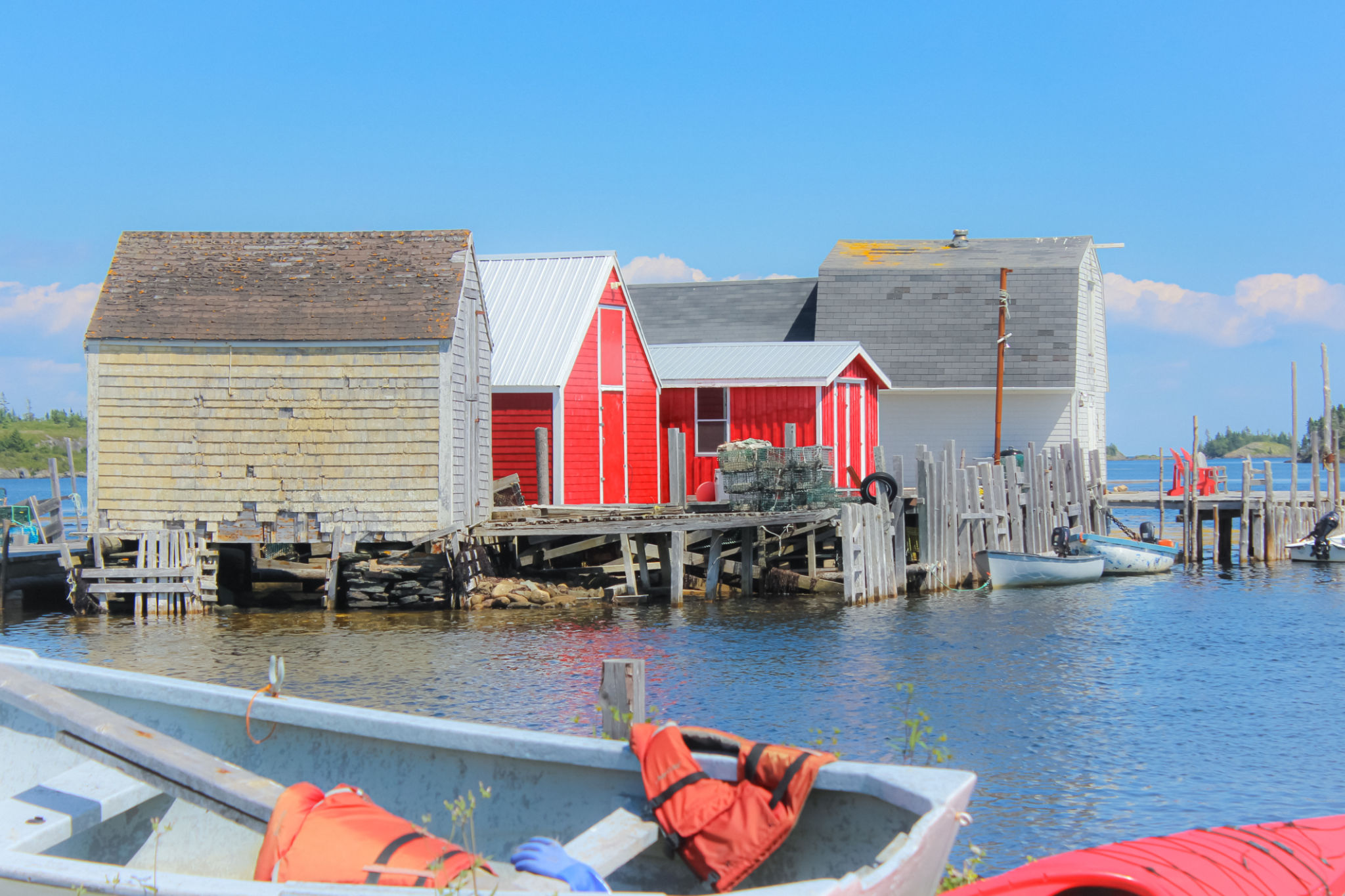
Misconception #4: Welding is Only for Large-Scale Projects
Many people believe that industrial welding is only suitable for large-scale projects, but this isn't true. Welding solutions are versatile and can be tailored to meet the needs of both large and small-scale projects. From constructing skyscrapers to repairing small machinery parts, welding plays a crucial role across various industries.
The adaptability of welding techniques makes them applicable in sectors such as automotive repair, maritime construction, and even art installations. This flexibility allows businesses of all sizes to benefit from reliable and durable welds.
The Importance of Debunking Misconceptions
Debunking these misconceptions is essential for businesses to leverage the full potential of industrial welding solutions. By understanding the complexities and capabilities, companies can make informed decisions that enhance productivity, safety, and cost-effectiveness.
In conclusion, industrial welding is a sophisticated field requiring expertise and precision. By dispelling myths around it, industries can better appreciate its value and utilize it effectively for various applications.